Periodic monitoring of the cooling tower fans with handheld devices proved risky, as fan faults could emerge between checks. The stress on mechanical components due to large rotating fans and varying operating loads could quickly escalate from emerging faults to catastrophic failure. Moreover, any gearbox or fan maintenance required a complete shutdown of the cooling tower, highlighting the need for 24/7 real-time condition monitoring.
To prevent this, the client reached out to our local distributor for a continuous vibration monitoring solution that allowed them to retain manual access to raw vibration data.
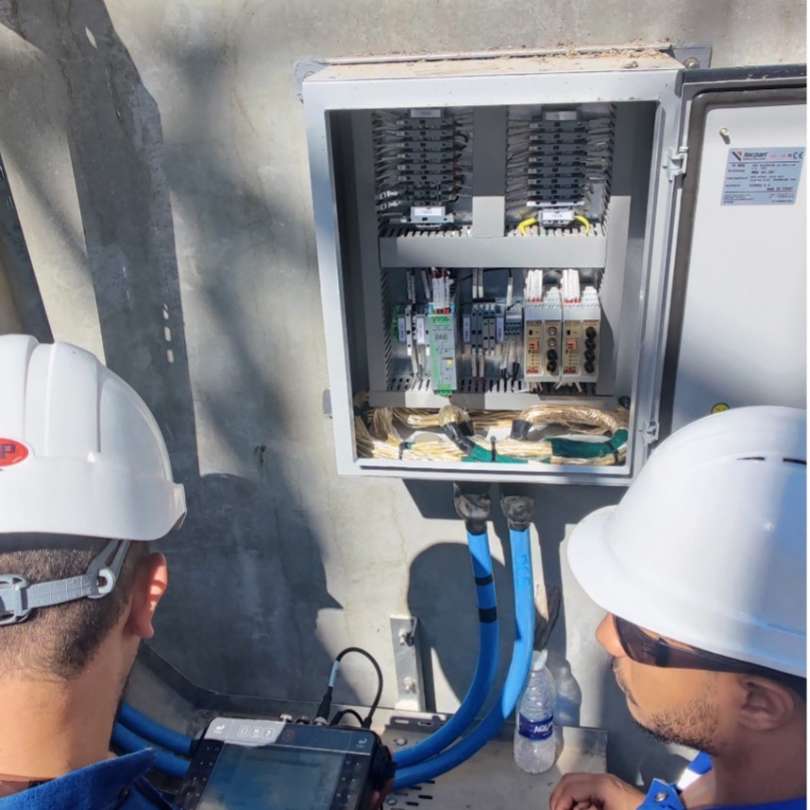
Our local distributor stepped in, implementing a continuous vibration monitoring solution. Each of the cooling tower cell’s four fans were retrofitted with permanently mounted vibration sensors, one on the gearbox input shaft, and one on the output shaft. All eight sensors were connected to two 4-channel PCH 1420 Vibration Monitors with buffered BNC outputs.
The client now receives continuous, conditioned 4-20 mA to their DCS for continuous, monitors the cooling tower fans in real time and easily detects imbalance, misalignment, unusual gear mesh frequencies, and bearing wear.
Simultaneously, vibration specialists can safely access raw vibration data with handheld devices for in-depth analysis. The buffered BNC outputs of the PCH 1420 prevent short-circuits and interruptions during manual checks. And because the PCH monitoring system is modular, the client can implement the solution one cooling tower cell at a time or as the budget permits.