Budget-friendly vibration monitoring for Flettner rotor sails
We have worked closely with leading rotor sail manufacturers to design a monitoring solution specifically for maritime Flettner rotors.
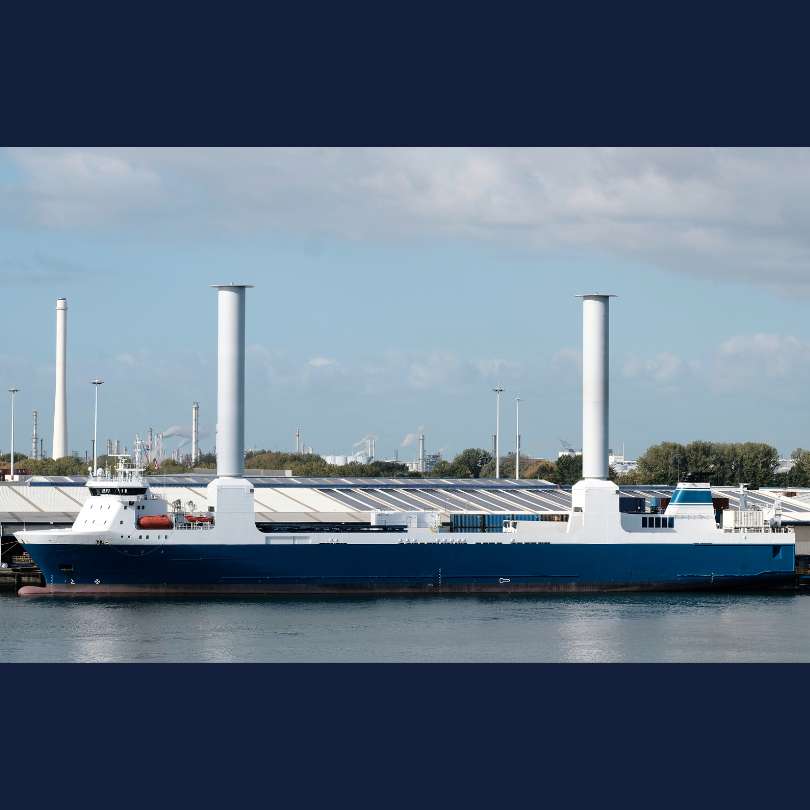
Applications
The monitoring solutions are suitable for rotor sails of any size on shipping vessels such as cargo ships and commercial vessels such as ferries.
Recommended solution: Structural vibration + bearing condition monitoring
We recommend measuring vibration in the upper support in three dimensions with a permanently mounted triaxial, low frequency MEMS accelerometer to monitor structural oscillation and imbalance. A one-axis, high-frequency accelerometer detects emerging bearing faults in the thrust and roller bearings and a tacho or analogue 4-20 mA speed sensor monitors RPM.
The rotor sail’s lower support roller bearings are measured using up to sixteen high frequency accelerometers (one sensor per bearing).
The two types of accelerometers enable you to capture the high frequency vibrations of emerging bearing faults as well as the low frequency vibration of structural oscillation and imbalance. The monitoring and trip alarms for both upper and lower bearings provide added safety.
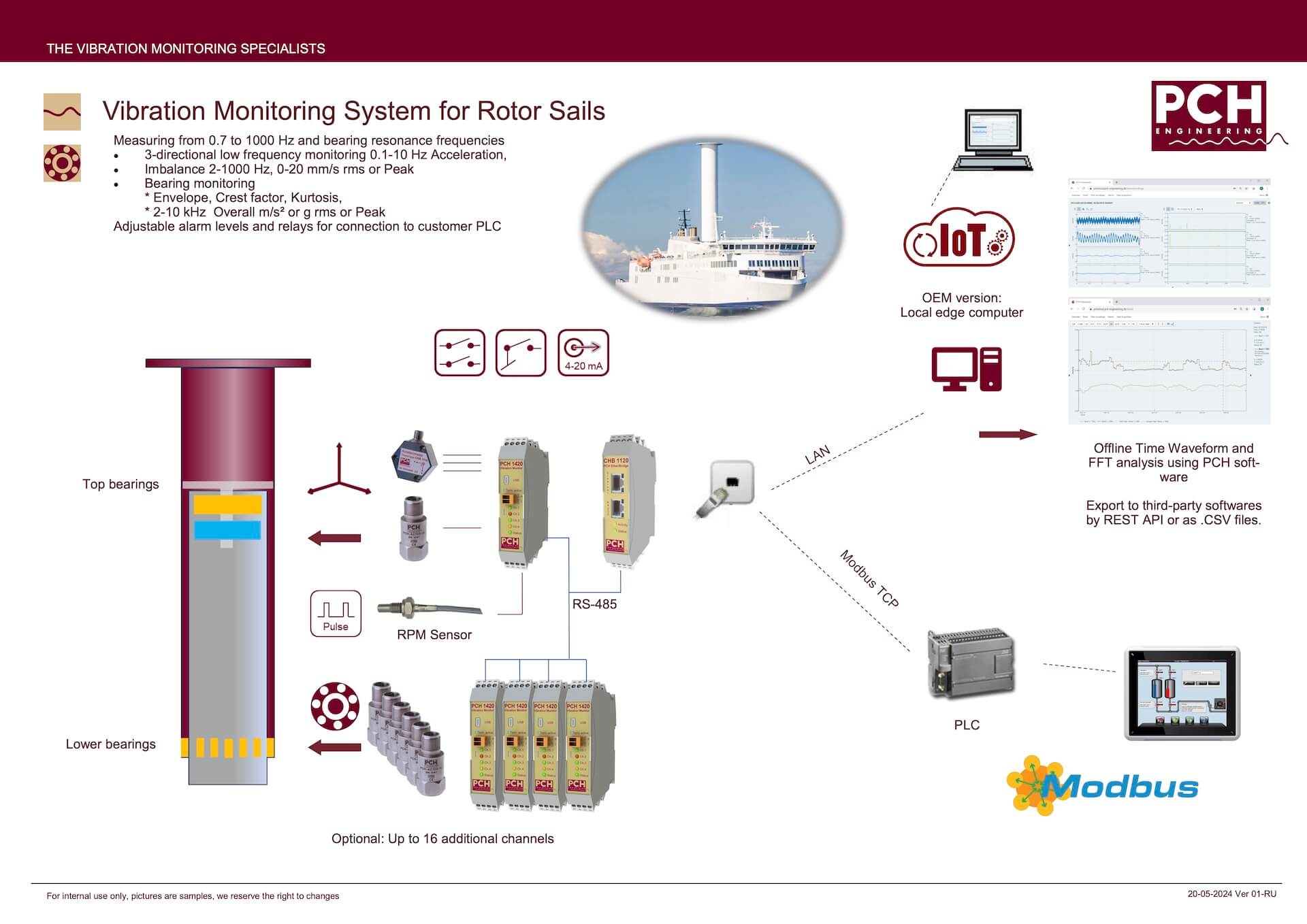
Depending on the number of bearings being monitored, three to four PCH 1420 Vibration Monitors provide Time Waveform files, scalar values of imbalance, Envelope Acceleration, Crest/Kurtosis and 2-10 kHz Acceleration Peak, as well as an alarm relay with trip alarms for safety shutdowns of the rotor sail.
The PCH EtherBridge communication device transfers vibration data to the local rotor controller, edge computer or PLC system for analysis. The local edge computer can generate and visualise FFT files and export customised Time Waveform and FFT files to third party software.
Components of the recommended solution
- Up to 5 PCH 1420 Vibration Monitors
- 1 PCH EtherBridge
- 1 CHB1126 triaxial MEMS accelerometer
- Up to 16 PCH-AC102 IEPE accelerometers, 100 mV/g
- 1 speed sensor
Basic solution: Monitor upper support bearings only
If your budget dictates only measuring one set of bearings, we recommend installing the triaxial MEMS accelerometer and the high frequency accelerometer on the upper support bearings. The upper bearings support the heaviest load and are subject to greater structural movement than the bearings of the fixed lower support.
The PCH 1420 Vibration Monitor and the PCH EtherBridge provide advanced data to the local rotor controller or PLC system.
Components of the basic solution
- 1 PCH 1420 Vibration Monitors
- 1 PCH EtherBridge
- 1 CHB1126 triaxial MEMS accelerometer
- 1 PCH-AC102 IEPE accelerometer, 100 mV/g
- 1 speed sensor
Contact our consultants and let them guide you to the right solution for your application
Contact
a sales consultant
PCH 1420 Vibration Monitor: 4 input channels for high- and low-frequency monitoring
The advanced, four-channel PCH 1420 Vibration Monitor continuously monitors structural vibration in three dimensions as well as the condition of the rotor sail bearings. Its built-in alarm relay with trip alarms and shutdown functionality provides added local safety on board the ship.
Three of the monitor’s four input channels receive data from the triaxial MEMS accelerometer CHB 1126, which measures low vibration frequencies in the upper support, detecting excessive rotor sail oscillation and imbalance. The fourth input channel receives data from a standard IEPE vibration sensor that monitors the condition of the upper support bearings.
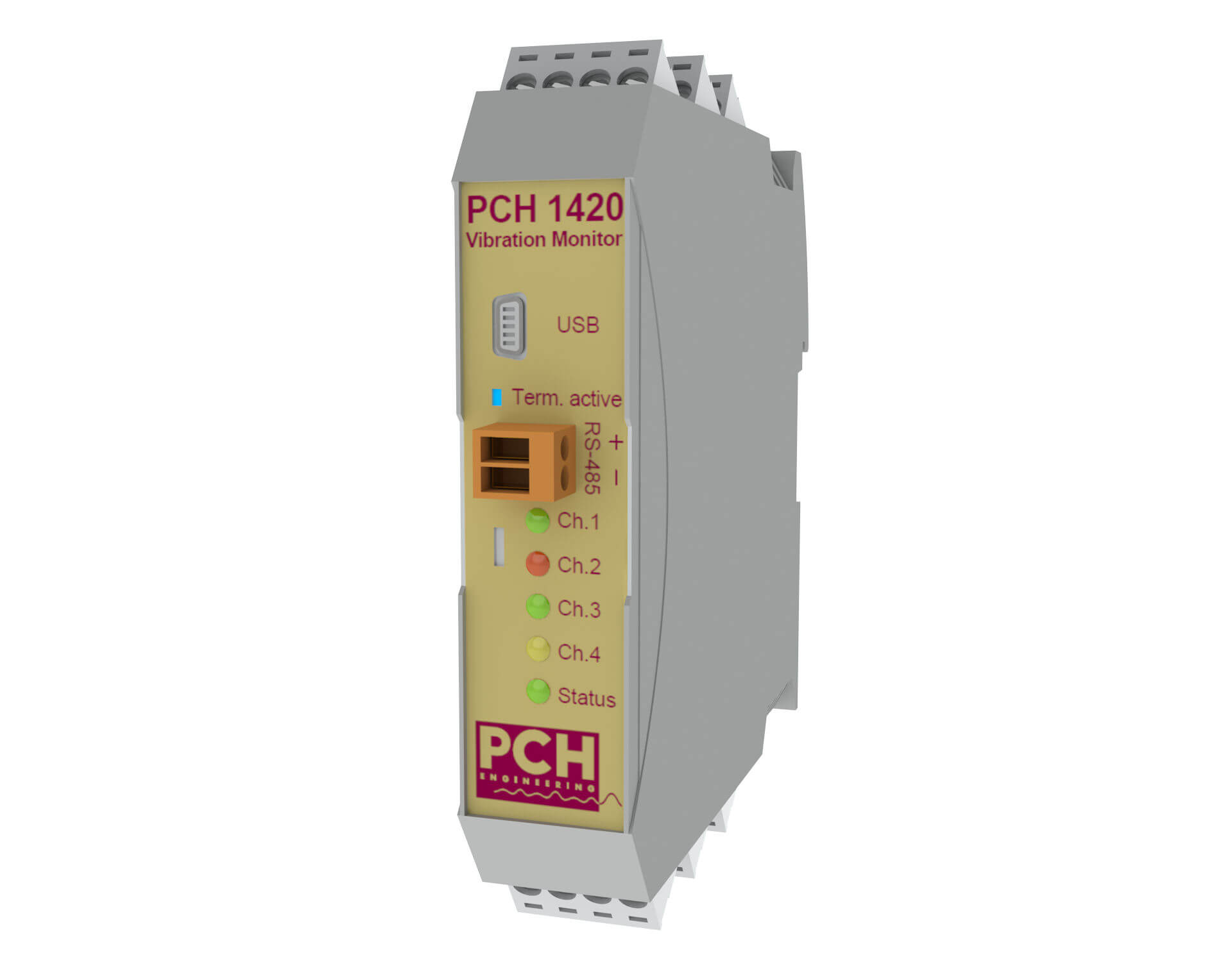
Features of the PCH 1420 Vibration Monitor
- Permanently mounted sensors
- Advanced local trip alarms
- Continuous monitoring of high and low frequencies
- Remote access to vibration data (FFT and Time Waveform)
- Seamless integration with local rotor controller or PLC systems
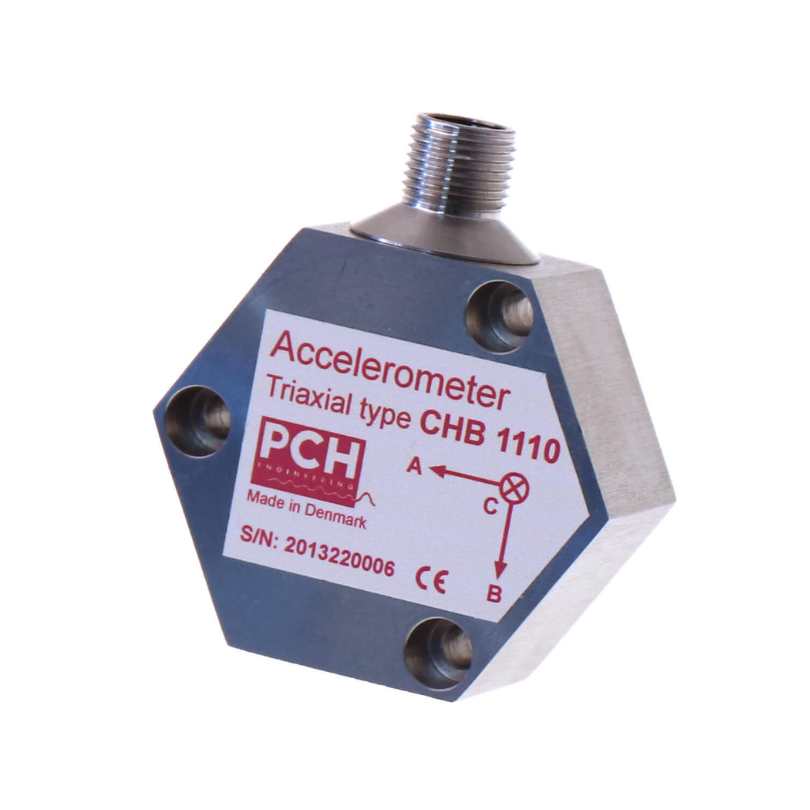
CHB 1126 triaxial MEMS accelerometer: Low-frequency sensor
- Triaxial monitoring: X, Y, Z
- Structural monitoring (low frequency vibration)
- Powered by the PCH 1420
- 100 mV/g sensitivity (or CHB 1110 for 300 mV/g)
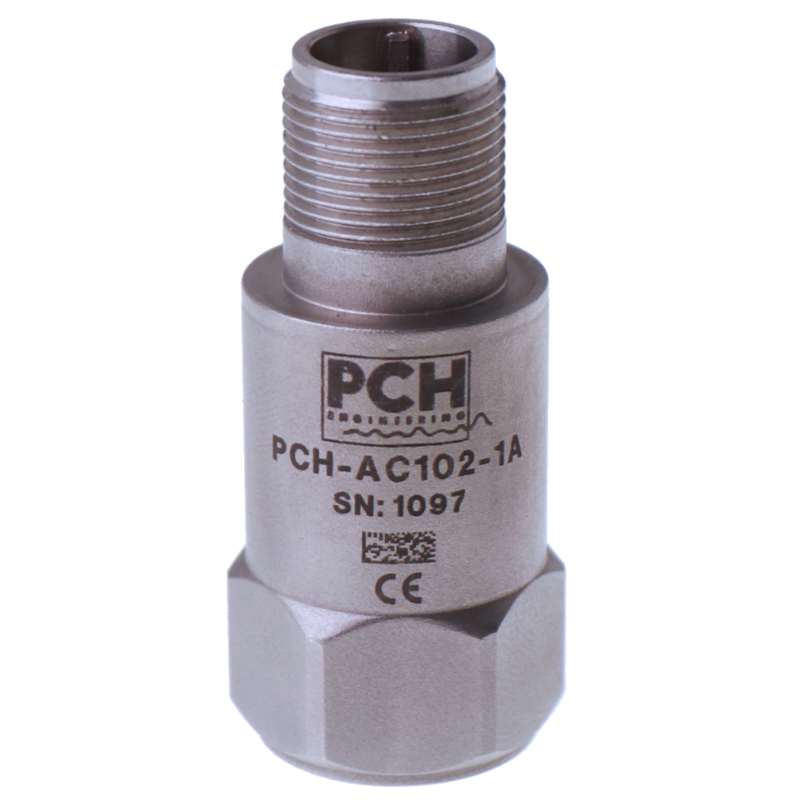
PCH-AC102 IEPE accelerometer: High-frequency sensor
- 1-axis monitoring
- High and low frequency vibration
- Enhanced bearing condition monitoring
- 100 mV/g sensitivity
PCH EtherBridge: Remote vibration monitoring
We combine the vibration monitor with the PCH EtherBridge to easily incorporate vibration data into your predictive maintenance strategy or OEM service offer. The PCH EtherBridge is a communication module that enables you to transfer rotor sail vibration data to a local rotor controller or programmable logic controller (PLC) for further analysis.
Features of the PCH EtherBridge
- Transfer vibration data automatically to a controller or edge computer
- Communication hardware: RS 485, RS 485/232, RJ45 LAN connector for TCP
- Communication protocols: Modbus TCP, Modbus RTU, OPC UA
Why monitor vibrations in rotor sails?
Vibration monitoring of rotor sails supports the maritime industry’s efforts to bring down greenhouse gas emissions and comply with international energy efficiency regulation.
Auxiliary wind propulsion by rotor sails can help vessels save up to 25 % fuel, but rotor sails operate in harsh conditions and require careful maintenance to ensure they function properly. Bearing wear and bearing failure can lead to operational disruptions and excess fuel consumption, while excessive structural oscillation can transmit significant vibrational energy to the structural components of the vessel due to the high mass of the large rotor cylinder.
Continuous, remote vibration monitoring of the rotor sail’s structure and bearings enables you to collect operational vibration data under load and predict the need for maintenance or rotor sail adjustments based on the condition of the bearings. With vessels at sea for up to several weeks at a time, you can schedule and carry out any necessary maintenance when the ship is in port and minimize unplanned downtime of the rotor sails.
Talk to us about monitoring solutions to avoid common rotor sail maintenance issues
Contact our
sales consultants
How to monitor vibration in rotor sails
The natural rolling motions of the ship and the rotational dynamics of the rotor sail become more pronounced closer to the top of the 15-30-meter-tall rotor cylinder. This makes monitoring in three dimensions necessary in order to accurately detect excessive structural oscillation and emerging bearings faults.
We recommend using a high-frequency IEPE accelerometer in combination with a low-frequency triaxial MEMS accelerometer to monitor the upper support bearings, as they take most of the structural load. Standard IEPE vibration sensors can be added to monitor the condition of the bearings of the fixed lower support.
Most common rotor sail maintenance issues
Structural oscillation
Rotor sails exert significant forces on the ship's structure, especially during high winds or rough seas.
As rotor sails are retrofitted, ensuring the structural integrity of both the rotor sails and the ship itself is crucial to prevent damage or accidents.
The movement of the ship and the rotation of the rotor sail produces low-frequency structural oscillation. However, excessive low-frequency vibration can be a symptom of a loose foundation or other structural problems such as overloading or mass imbalance.
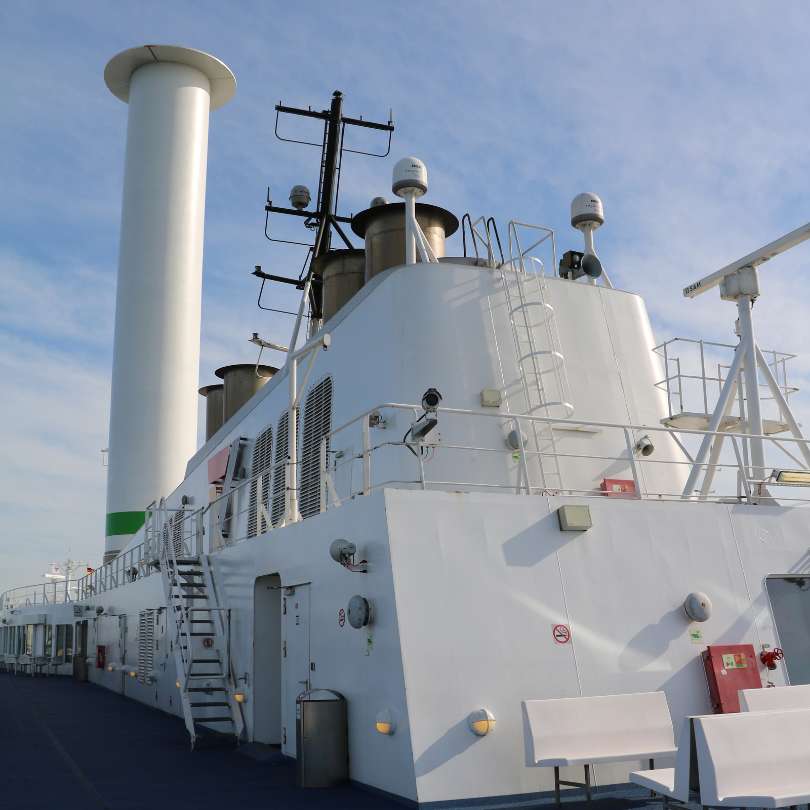
Mass imbalance
Mass imbalance can occur either at the topmost Thom disk if it is offset from the rotation axis during installation, or at the mid-plate, which has a higher mass concentration than the rotor.
Overloading
High winds or heavy cargo can overload the rotor sail motor and put too much strain on the bearings. By monitoring the condition of the bearings, you can detect emerging bearing faults and shut down the rotor motor in the event of overload.
Bearing faults
The upper and lower support bearings of a rotor sail are critical to its proper operation. The harsh environment of the sea with its fluctuating winds and saltwater spray increases the risk of bearing wear and corrosion, which can lead to bearing failure. Incorrect lubrication can exacerbate the problem.
Drive imbalance
Accumulating wear and dirt can lead to imbalance of the rotor sail drive. This creates excessive vibration, which is picked up by the vibration sensors on the bearings.