Recommended vibration monitoring system for cooling towers
At PCH Engineering, we offer various levels of protection to fit your needs and budget, from a simple sensor and switch setup with one measuring point to advanced, IoT condition monitoring with multiple measuring points.
We recommend you monitor the rotating components of cooling towers continuously with permanently mounted vibration sensors and online access to vibration data.
Contact
a consultant
Setup 1: Cooling tower sensor and electronic switch
PCH 1270 and PCH 1272 (RS-485) are compact vibration monitors with a built-in vibration sensor (accelerometer), a 4-20 mA output, and digital switch functionality for local safety. The switch can be validated electronically.
The compact monitors are suitable for low frequency monitoring and emergency shutdown of the cooling tower motor. More monitors can be mounted individually to provide more than one measuring point.
PCH 1272 also offers RS-485 communication for online data access via
PCH EtherBridge.
Click the image to enlarge it
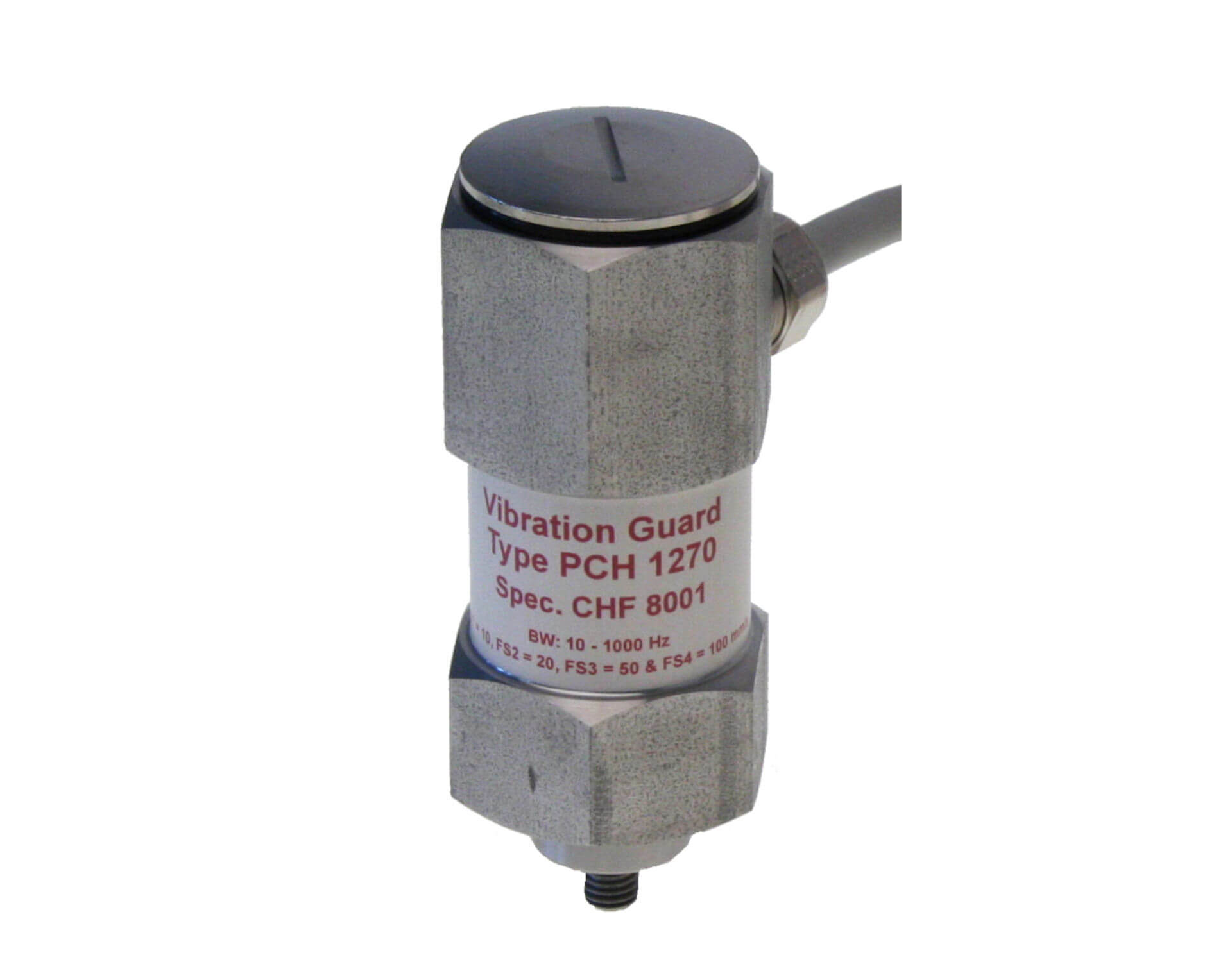
PCH 1270 and PCH 1272 vibration monitors
- Frequency range: select between 0.7/1/2/3-300/1000 Hz
- Measuring range: adjustable with DIP switches: 0-10, 0-20, 0-50 or 0-100 mm/s or m/s²
- Signal detection: RMS
- Measuring parameter: velocity (mm/s) or acceleration (m/s²)
- Outputs: 1 analogue output (4-20 mA), 2 alarm relays
- Compliance: SIL 2, IEC61508, PL-d, IP 66/68 (for ATEX, see PCH 1275/1277)
- Communication (PCH 1272 only): RS-485 via PCH EtherBridge, IoT-ready, PCH Cloud
Setup 2: Thorough condition monitoring with multiple measuring points
The PCH 1420 vibration transmitter monitors the vibration levels measured by vibration sensors on the cooling tower fan, bearings and gearbox.
One PCH 1420 vibration transmitter can cover up to four measuring points on one cooling tower or one measuring point on four different cooling towers.
Real-time data can be accessed remotely through various communication protocols.
PCH 1420 is ideal for Industry 4.0 environments and is part of the modular
PCH Link Concept.
Click the image to enlarge it
PCH 1420 vibration transmitter, IoT-ready
- Frequency range: adjustable, 0.7 Hz to 11.5 kHz
- Measuring range: adjustable (default 0-20 mm/s and 0-100 m/s²)
- Signal detection: RMS, Peak, Peak to Peak
- Measuring parameter: velocity (mm/s), displacement (μm/mm) or acceleration (m/s²)
- Outputs: 4 analogue outputs (4-20 mA or 0-10 V DC) or 4 digital outputs, 1 main relay, additional input channels available via PCH Input Box
- Communication: RS-485, USB, IoT-ready, PCH Cloud, Modbus via PCH EtherBridge
- Compliance: SIL 2, IEC 61508, PL-d, IP 20
Setup 3: Cooling tower condition monitoring with additional buffered outputs
With the PCH 1420 with buffered outputs, your vibration specialists can access raw vibration data with handheld devices for more advanced on-site measurements.
The PCH 1420 with buffered outputs is suitable for Industry 4.0 environments and provides remote, online access to vibration data in real time when paired with the
PCH EtherBridge IoT communication module.
Click the image to enlarge it
PCH 1420 with buffered outputs: Advanced, IoT condition monitor for cooling towers
- Advanced, IoT condition monitor for cooling towers
- Frequency range: adjustable, 0.7 Hz to 11.5 kHz
- Measuring range: adjustable (default 0-20 mm/s and 0-100 m/s²)
- Signal detection: RMS, Peak, Peak to Peak
- Measuring parameter: velocity (mm/s), displacement (μm/mm) or acceleration (m/s²)
- Outputs: 4 digital or analogue outputs (4-20 mA or 0-10 V DC), 4 buffered outputs, 1 main relay, additional input channels available via PCH Input Box
- Communication: RS-485, USB, IoT-ready, PCH Cloud via PCH EtherBridge
- Compliance: SIL 2, IEC 61508, PL-d, IP 20
Case: Ensuring cooling tower safety in Egypt
See how this alkylbenzene plant enhanced safety by combining periodic, handheld measurements with continuous monitoring using the PCH 1420 with buffered outputs.
Related monitoring modules for added functionality
PCH 1420 vibration monitor and PCH 1420 with buffered outputs are both part of our modular condition monitoring system,
PCH Link Concept. You can combine the modules in the system with the PCH 1420 monitors to fit your needs.
For cooling tower monitoring, we recommend you add an EtherBridge communication module for online data access and IoT compatibility.
The PCH Input Box provides even more data to help you keep your cooling towers safe.
PCH EtherBridge communication module: Online data access and IoT compatibility
Combined the PCH EtherBridge with the PCH 1420 or PCH 1420 with buffered outputs and get online access to vibration data in real time. You or your service provider can analye the condition of the cooling tower parts remotely and schedule maintenance when needed.
- Relays: 1 alarm relay and 1 digital input relay
- Communication hardware: RS 485, RS 485/232, RJ45 LAN connector for TCP
- Communication protocols: Modbus TCP, Modbus RTU, OPC UA
- Data storage: PCH Cloud, IIoT Rest, mini SD-card (optional)
PCH Input Box: Monitor fan RPM, motor kW and more
The PCH Input Box can be added to any PCH 1420 vibration transmitter, expanding the monitoring to include fan RPM, motor kW, wind speed m/s, wind direction or even basin water depth from a level meter.
Monitoring wind and RPM conditions in addition to vibrations enhances the total protection of the system and provides more profound knowledge of the condition of the cooling tower.
24-hour cooling tower protection
All PCH cooling tower monitoring equipment monitors your cooling tower 24/7 and is easily retrofitted to any cooling tower make and type in accordance with the instructions of the tower manufacturer.
Our consultants can help you find the proper vibration monitoring setup for your specific cooling tower facility.
Contact
a consultant
Why monitor vibrations in cooling towers continuously?
Often, cooling towers are only monitored periodically with handheld devices, while local safety relies on a mechanical vibration switch to shut down the motor in the event of impending failure.
This may seem like a cheap and simple solution. However, it can be a risky strategy. Here is why:
Mechanical switches can be unreliable
Over time, mechanical switches can become unreliable due to corrosion.
There is no easy way to validate the mechanical switch, so you won’t know it is broken until the fan or gearbox fails.
And even when the switch does work, secondary damage has often been done before the machinery is shut down.
Risk of failure between checks
The large rotating fans and varying operating loads of cooling towers put great stress on the mechanical components. Defects can go from emerging faults to catastrophic failure in minutes.
With periodic monitoring, faults might go undetected between checks. This can lead to breakdowns, costly, unscheduled production stops, and worst-case scenario, catastrophic failure and secondary damages.
Add to this that any maintenance of the gearbox and fan requires a complete shutdown of the cooling tower, and you have a strong case for 24/7, real-time condition monitoring of your cooling tower.
Reduced maintenance costs and longer machine life
Continuous vibration monitoring with permanently mounted vibration sensors and online access to data in real time enables you to monitor the condition of the cooling tower equipment round the clock.
You can detect faults before they lead to serious performance issues, and prevent unplanned production stops or outright machine failure.
This will not only drive down maintenance costs and the cost of production stops. It will also extend the life of your cooling tower machine components, reducing the overall cost of ownership.
Start protecting your cooling towers today:
Contact
a consultant
How to monitor vibrations in cooling towers
Permanently mounted vibration sensors measure vibrations on the rotating parts of the cooling tower: the fan, shaft and gearbox.
Excessive vibrations or vibrations outside the normal pattern for the machinery indicate an emerging defect. A trained vibration specialist can analyze the vibration patterns and frequencies and determine the root cause of the problem before it leads to machine failure.
Where to mount vibration sensors on cooling towers
You can choose one measuring point or multiple. The more measuring points (i.e., the more sensors), the more data you collect, and the more information you have on the condition of the cooling tower machinery.
Mounting of one measuring point
If you have only one measuring point, mount the sensor as close to the gearbox output shaft as possible.
With a compact monitor such as the PCH 1270 or 1272, the sensor is built into the transmitter.
This is a cost-effective solution if you want just one measuring point, but also want the safety provided by continuous, 24-hour monitoring.
Mounting of multiple measuring points
If you have multiple measuring points in your setup, mount sensors on the fan bearings and the input and output bearing housing of the gearbox.
Radial and axial positions should be considered.
This helps you monitor the condition of the fan, the fan blades, the motor shaft, the bearings and the gearbox, enabling you to detect and prevent serious damage from bearing faults, imbalance and misalignment, fan blade imbalance, gear mesh wear etc.
Contact a consultant
to learn more
Most common causes of cooling tower failure
Varying load conditions with cooling tower machinery running at peak load for short periods of time can degrade machine performance and wear out the rotating parts of the cooling tower machinery.
The mechanical parts of the cooling tower, the fan blades, shaft, gears, and bearings, are all subject to wear over time. This can cause excessive vibrations, which may be a sign of impending failure.
The most common cooling tower faults are:
- Fan failure
- Bearing failure
- Gearbox failure
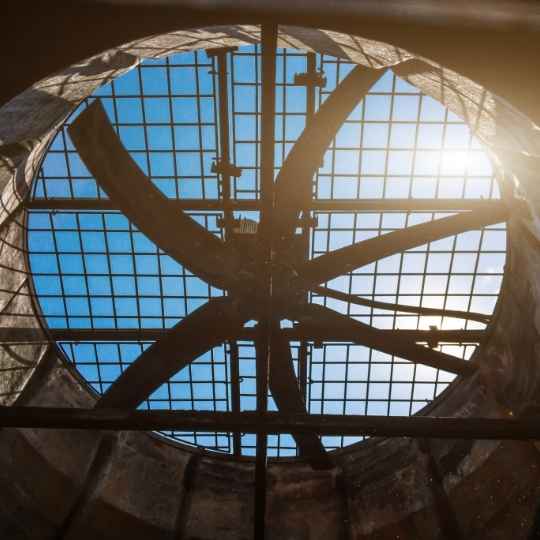
Fan failure
The fan may fail due to unbalanced fan blades or errors in the blade pitch. These cause excessive vibrations and may lead to secondary damage such as bearing failure.
Bearing failure
The bearings take the brunt of the varying loads, and they generally have a shorter lifespan than the rest of the machinery.
Detecting bearing faults at an early stage is crucial to preventing machine breakdowns and extending machine life.
Gearbox failure
The gearbox transfers energy from the motor to the fan. It is placed at the top of the cooling tower and is impossible to access unless the cooling tower is shut down.
The airflow and moisture levels at the top of the cooling tower also put stress on the gearbox.
Other gearbox failure causes may be misalignment of the shaft between gear and motor, wear on the gear teeth, or bearing defects.
Protect your cooling tower from common defects with vibration condition monitoring.
Contact
a consultant