Recommended vibration monitoring system for hydroelectric turbines
We recommend that you choose a vibration monitoring solution with online vibration data access such as the PCH 1420 vibration monitor for your hydroelectric power station.
This solution provides local safety in the form of adjustable alarms and shut-down functionality while allowing you to integrate real-time vibration data into the plant’s predictive maintenance strategy.
Remote access to vibration data also means you can centralise or outsource maintenance of your hydropower equipment.
Contact
a consultant
PCH 1420: Advanced IoT vibration monitor for hydro turbine condition monitoring
- Frequency range: adjustable between 1-10,000 Hz
- Signal detection: RMS, Peak, Peak to Peak
- Measuring parameter: velocity mm/s, displacement (µm/mm) or acceleration g, m/s2
- Outputs: 4 configurable outputs (relays or 4-20 mA/0-2.4, 5, or 10 V), 2 alarm relays, buffered outputs optional
- Communication: RS-485, IoT-ready, PCH Cloud
- Compliance: SIL 2, IP 20
- Sensor options: Versions available for Eddy Current/proximity probes, IEPE accelerometers, and electrodynamic velocity sensors
Setup options customised to your hydro-electric power plant
The advanced PCH 1420 vibration monitor is the cornerstone of our modular condition monitoring system, PCH Link Concept.
You can add modules from this series to adjust the monitoring solution to your hydro power equipment and monitoring needs.
Below we have sketched examples of possible setups.
Example of hydro turbine monitoring with local HMI
Click the image to enlarge it
Example of hydro turbine monitoring with IoT condition monitoring
Click the image to enlarge it
Example of hydro turbine monitoring with buffered outputs
Click the image to enlarge it
Why monitor vibrations in hydro turbines?
Hydroelectric power generation equipment is subject to massive forces. This causes vibrations, which can wear down turbine parts and ultimately cause machine breakdowns, in some cases with disastrous results.
Historically, hydro turbines were monitored at regular intervals. Often, they were operated under baseload conditions only, and maintenance was either corrective or preventive. In other words, machine parts were repaired or replaced either before it was necessary, ramping up the maintenance costs, or after they broke down, resulting in costly, unscheduled production stops.
However, there is a growing need for predictive maintenance in hydro power plants. Here is why:
Increasing productivity demands
Demands for productivity and continuity of production have increased, which means that hydro turbines are often operated at partial-load conditions, sometimes in rough zones.
Greater stress on machines
Some new machines are less robust, and machine life of older hydro units is extended through refurbishments, putting greater stress on the machinery.
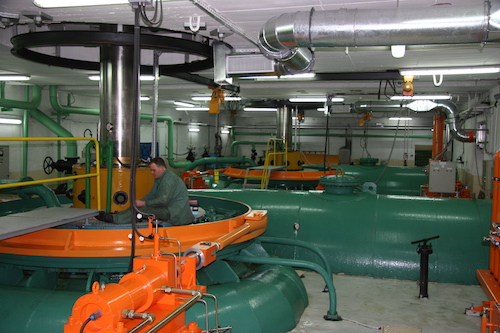
Benefits of monitoring vibrations in hydro power equipment
Research shows that, by monitoring the vibration levels of the hydroelectric power generation equipment continuously using an online condition monitoring solution such as the PCH 1420 vibration monitoring system, you can:
- make maintenance-decisions based on the machine condition
- ensure a stable production of power
- safeguard on-site personnel
- reduce maintenance costs
- prevent serious machine damage
- minimize the outage frequency
- extend machine life
- enhance machine efficiency.
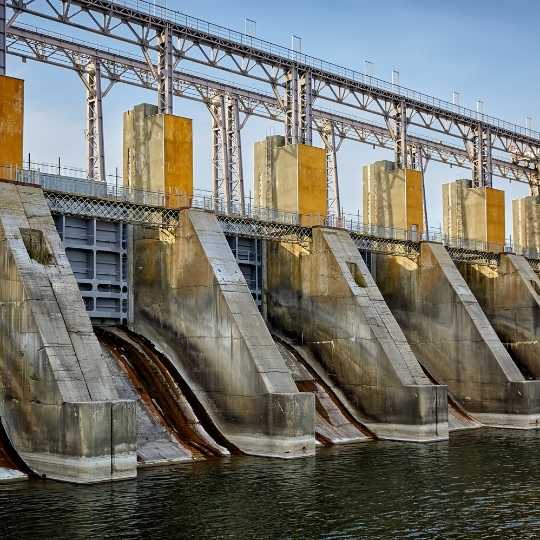
Cost-benefit analysis of condition monitoring in hydro power plants
Another study has shown that the cost of installing an online condition monitoring solution in hydroelectric power plants is far outweighed by the benefits:
- Maintenance costs decrease by 50–80%
- Equipment breakdowns decrease by 50–80%
- Machine downtime decreases by 50–80%
- Overtime costs decrease by 20–50%
- Machine life increases by 20–40%
- Profits increase by 25–30%
Start protecting your hydroelectric power generating units today:
Contact
a consultant
How to monitor vibrations in hydraulic turbines
You can monitor vibrations in all types of hydroelectric water turbines, whether they be impulse turbines such as Pelton wheels, turgo turbines and crossflow turbines; or reaction turbines such as propeller/Kaplan turbines, tube turbines, Francis turbines, bulb turbines or straflo turbines.
Note changes in vibration patterns
The hydroelectric turbine will always vibrate to some degree due to mechanical, hydraulic and electrical factors. Each component generates a specific vibration frequency. If the vibration pattern of a turbine or generator component changes, this can be a sign of wear and early fatigue.
Excessive turbine and generator vibrations can, in and of themselves, accelerate the wear on the hydro power equipment, which can lead to machine damage and breakdowns.
By monitoring trends in the vibration data, you can map the vibration pattern of each individual hydro turbine and respond adequately to changes in the pattern.
Why use online vibration monitoring
To avoid unscheduled production stops and premature replacement of parts, we recommend you monitor vibrations in hydro turbines using an online vibration condition monitoring solution.
With online vibration monitoring, you can monitor relative shaft vibration, absolute bearing vibrations, turbine cover vibration, axial thrust position, stator core vibrations, stator bar vibrations, and stator end winding vibrations in the hydraulic turbine and hydroelectric generator.
Vibration data can be stored in the cloud for remote analysis and form part of a modern, IoT-based condition monitoring solution.
You can supplement the constant monitoring of rotating parts with non-contact proximity probe monitoring of the generator/turbine shaft vibration relative to the sleeve bearings.
Where to mount vibration sensors on hydropower turbines and generators
Vibration sensors such as low-frequency accelerometers are mounted on the casing of the turbine and generator near the bearings and shaft.
Eddy Current probes / proximity probes are used as non-contact sensors for monitoring sleeve bearings and are mounted in a radial position in the X and Y directions of the shaft (the X direction if applicable in the turbine construction).
Contact a consultant
to learn more
Most common defects in hydro turbines
There are various reasons why decanter centrifuges fail. Gradually increasing vibrations may indicate wear and imbalance of the components, whereas suddenly occurring vibrations may indicate part breakage, chipping or bearing failure.
The most common hydro turbine faults are:
- Cavitation
- Imbalance
- Shaft misalignment
- Bearing faults
- Soft-foot problems
- Eccentricity
- Rotor inter-turn faults
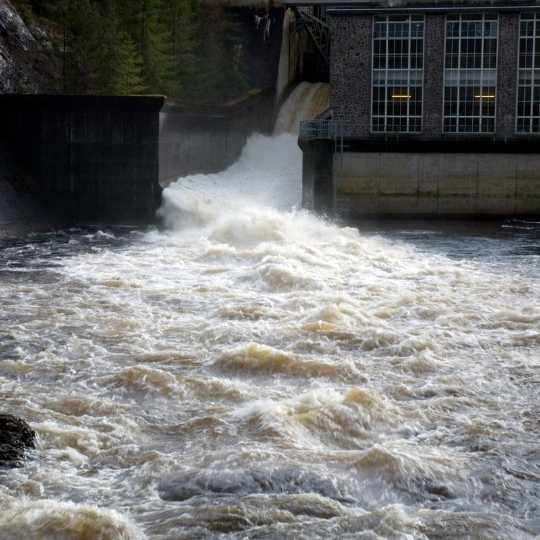
Cavitation
When bubbles form in the water, the pressure changes, which results in noise or vibration in the water column.
As the bubbles implode against a hard surface such as a hydraulic turbine, the cavitation can cause erosion and reduce the turbine capacity and efficiency pressure.
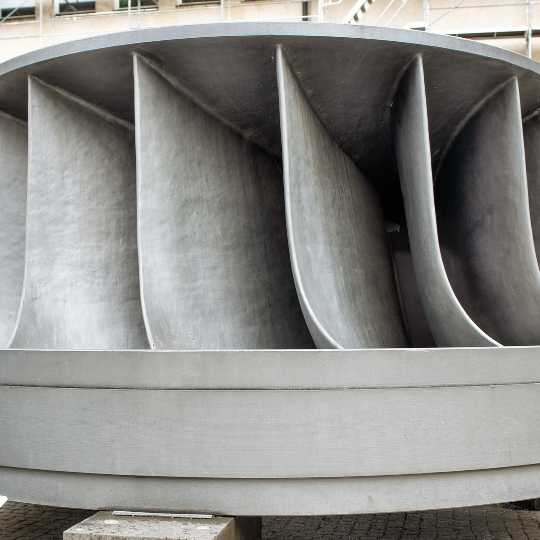
Imbalance
Imbalance occurs when the weight of the rotors of the hydro turbine or hydro generator are unevenly distributed.
This can be due to, e.g., misalignment, eccentricity, distortion, corrosion, wear, deposit build-up etc.
Imbalance tends to cause radial vibrations that increase with rotational frequency.
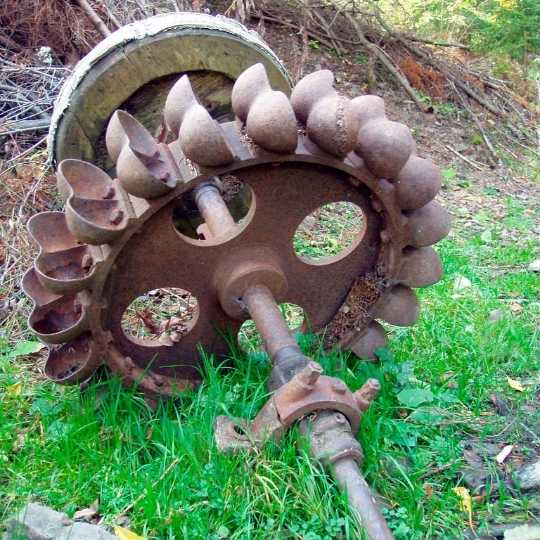
Shaft misalignment
Misalignment of the hydro turbine shafts causes axial and radial vibrations, which increase with rotational frequency.
Shaft misalignment can cause bearing failure and overheating as well as breakage of the wicket gate linkage.
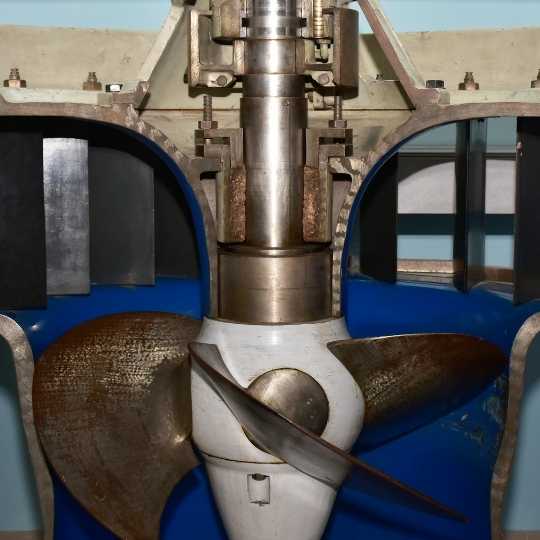
Bearing faults
Hydro turbine bearings are subject to normal wear and erosion and often have a shorter life span than the rest of the hydro turbine and generator.
By monitoring the bearing vibrations, you can schedule maintenance in advance and replace the bearings based on their condition.
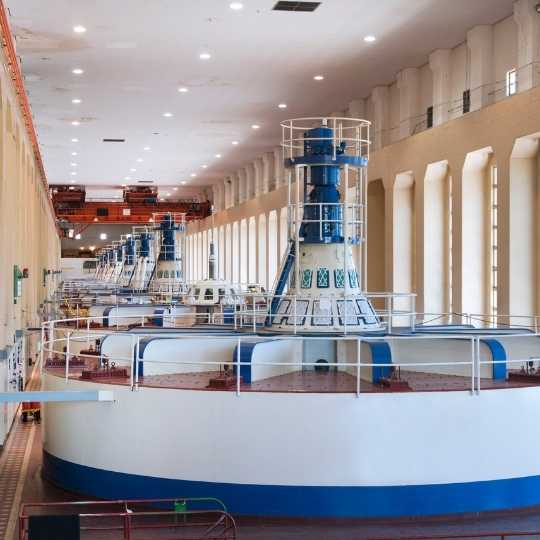
Soft-foot problems
Soft-foot problems are caused by the hydro turbine feet not being coplanar to the base or not being installed properly.
A poor foundation causes excessive vibrations in the hydro turbine, and the machine consumes more electrical power and degrades.
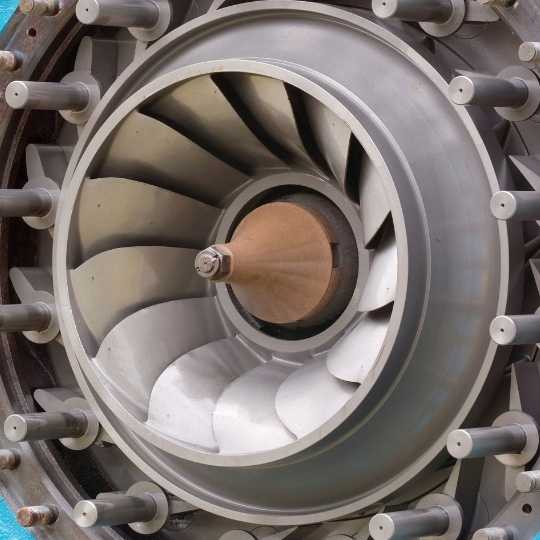
Eccentricity
Eccentricity is when there is a fluctuating air gap between the rotor and stator in the hydro generator.
The eccentricity can be either static or dynamic. If the eccentricity is not remedied, it can cause stator-winding faults due to mechanical abrasion of the stator insulation.
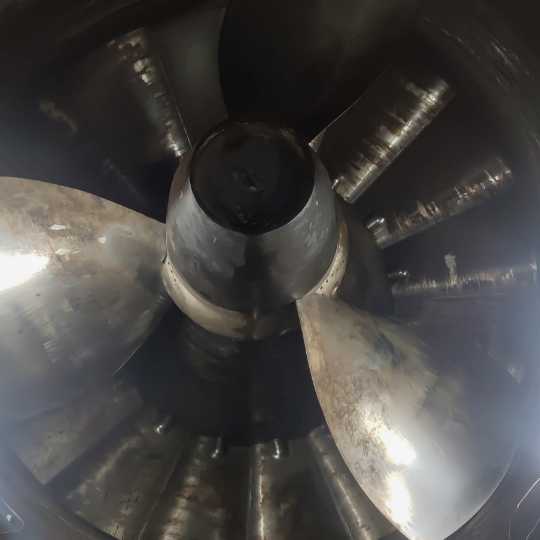
Rotor inter-turn faults
Inter turn faults in hydro generator rotors cause rotor earth faults, overheating and imbalance.
The unequal current in windings creates an uneven magnetic field, increasing the vibration frequency.
Protect your hydro turbine from common defects with vibration condition monitoring.
Contact
a consultant